Container Centralen
Container Centralen (CC) is a European market leader in reusable transport items (RTIs), known for their CC pool system. In order to guarantee good logistics, efficiency is extremely important and a good scanning device is essential for this. Container Centralen's wish was to replace the current, outdated scanner.
Within 4 months, Quatronic created a new RFID scanner app that tracks 4 million RFID-registered RTIs for more than 20,000 customers. In addition to an improvement in efficiency and reliability and flexibility in use, the in OutSystems application developed a solid basis for innovation.
Who is Container Centralen?
Container Centralen is a European market leader in the field of reusable transport items (RTIs). The company is known for their CC pool system, the largest pool system in the field of RTIs. More than 20,000 horticultural growers and suppliers of fresh produce use the RTIs to transport their goods to retailers, after which retailers use the transport items to display their products. By supplying standardized containers, trollies and stackable shelving units, Container Centralen can organize the entire logistics process efficiently and sustainably, so that the costs for the customer are also as low as possible.
The challenge
In order to properly set up the pool system logistically, efficiency is extremely important and a good scanning device is essential for this. When it became known that the software running the scanning device was out of date, it was urgent to find a solution that could be built within six months. In addition, it was desirable that the depot staff could also carry out other actions in addition to scanning, and it should also be possible to register not only the amount of goods received, but also their composition.
After a brief exploration of the problem through our standardized Design Sprint, this challenge was translated into the following evaluation criteria:
- Delivery of an MVP on top of the existing scanner;
- Application functionality without network coverage;
- Integration with the customized logistics system 'LogLink';
- Evidence of speed of development;
- Guarantee of maintenance and ease of use.
We now have a solid basis and the flexibility needed to continuously innovate.
Our approach
With a team of three consultants, we started working in two-week sprints. At the end of each sprint, the progress was presented to the people involved within Container Centralen, so that they could immediately include their feedback during development.
Three months after the start of production, Container Centralen received a fully integrated prototype at their depot in Hazerswoude (NL). After a successful pilot phase, mainly focused on usability improvements, the new RFID scanner app went live a month later and the supplier of transport items started a European training program.
The entire application has been set up in OutSystems, the number 1 low-code platform. The conveniences and flexibility that this low-code environment offers us has enabled us to focus strongly on properly analyzing the needs of Container Centralen and coming up with appropriate solutions. As a result, we were able to set up the RFID scanner app very quickly with all desired integrations and it fits perfectly with Container Centralen's business operations.
The result
In addition to replacing the old scanner with updated software, the new app has provided numerous improvements, including:
- Scan faster: users can now scan standard RTI configurations instead of multiple components;
- The ability to record the differences between packing slips and actual deliveries;
- Users can register damaged items and initiate repair orders;
- The RFID scanner app can be used for inventory.
.png)
These changes contribute to improved efficiency and reliability of the result. Recording anomalies and details of damaged items at the time of delivery makes a huge difference. It prevents surprises and discussions later and allows the organization to charge customers for missing items if necessary. In addition, the repair process works better, as Container Centralen immediately knows what activities are necessary once a delivery has been processed.
Container Centralen is now working on the development of the next innovation, which automatically monitors whether organizations return the packaging in good condition. It is also being investigated whether a simplified scanner app can be developed for customers. The creation of a next-generation logistics information system using OutSystems is even being considered. All this is to further increase the efficiency and sustainability of Container Centralen.
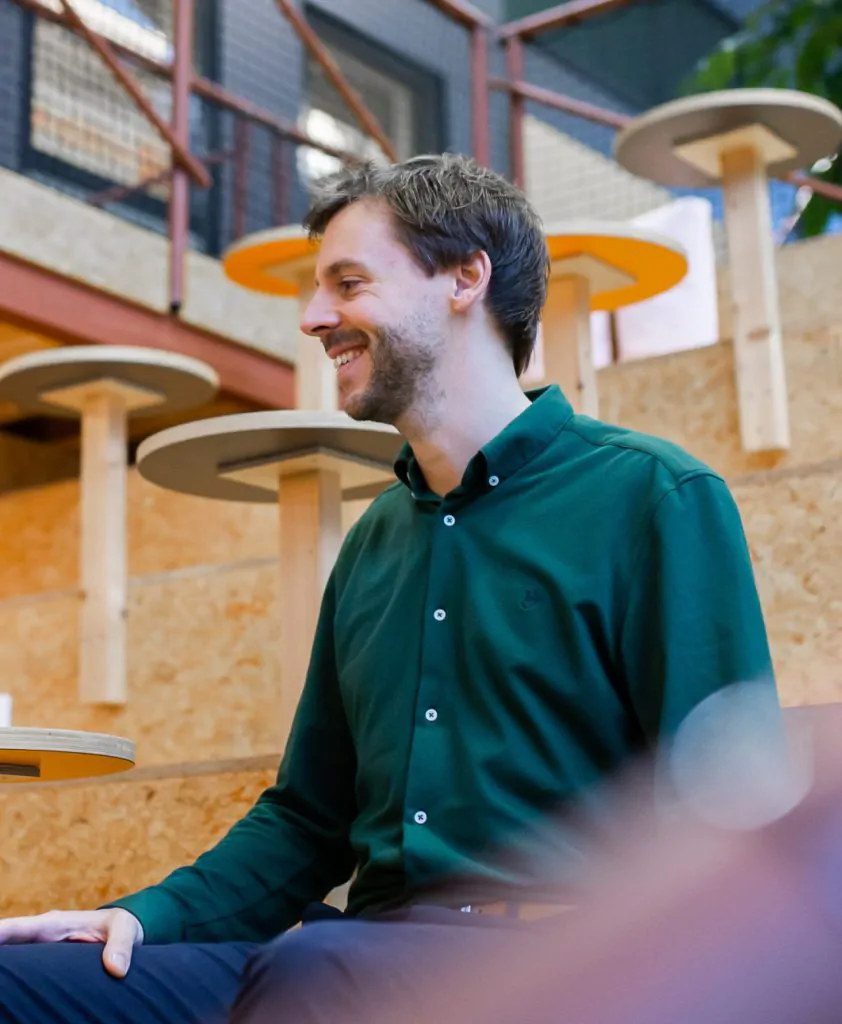